Michelin Uses 3D Printing to Realize Ambitious Sustainability Goals
Last year, Michelin debuted its sustainable 3D printed concept tire, called the Vision, at the Movin’On conference, which focuses on sustainable solutions for the automotive industry. This year’s conference is now in full swing, and Michelin has already made a bold announcement: it plans to see that by 2048, all of its tires are made with 80 percent sustainable materials, and that they are 100 percent recycled.
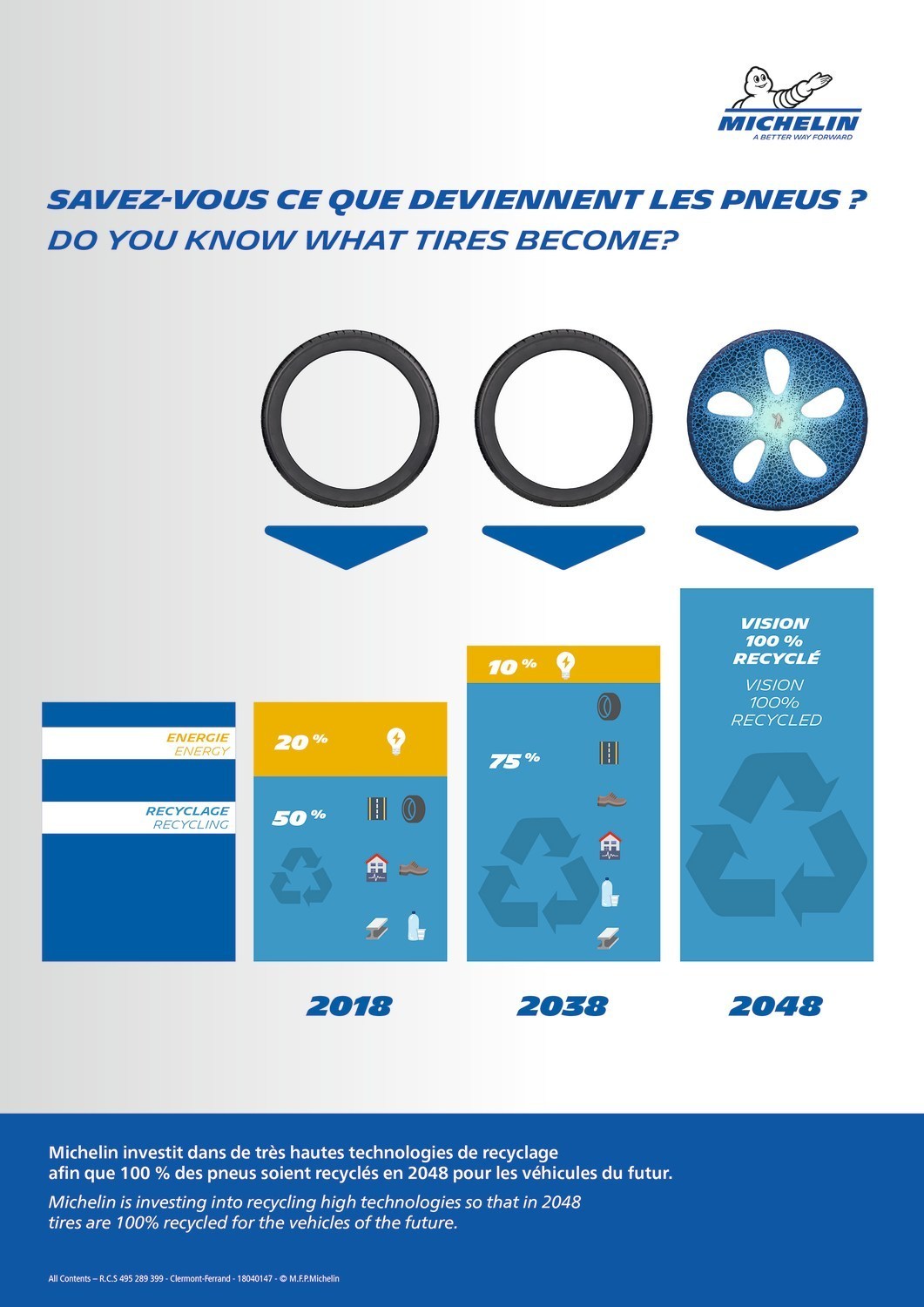
(PRNewsfoto/Michelin)
Tires aren’t doing too badly when it comes to the environment: the worldwide recovery rate is 70 percent and the recycling rate is 50 percent. In comparison, 14 percent of plastic containers or packages are recycled every year, and the car industry has a target recycling rate of only 3.5 percent. Currently, Michelin’s tires are made using 28 percent sustainable materials, which consist of 26 percent bio-materials like natural rubber, sunflower oil or limonene, and 2 percent recycled materials such as steel or recycled powdered tires. To increase this number to 80 percent, Michelin is turning to advanced technologies like 3D printing.
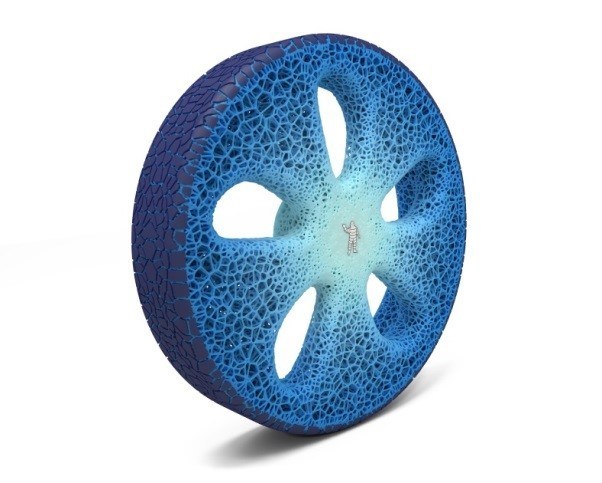
(PRNewsfoto/Michelin)
Michelin will work with its partners to develop advanced technologies and materials, and will take advantage of research programs like Biobutterfly, which was launched in 2012 by Michelin, Axens and IFP Energies to develop synthetic elastomers from biological materials like wood, straw, or beets. Michelin also recently acquired Lehigh, which specializes in high tech micro powders derived from recycled tires. Lehigh is a market leader in Micronized Rubber Powders (MRP), a sustainable raw material that reduces feedstock by up to 50 percent.
“This acquisition demonstrates Michelin’s strategic determination to capitalize on its expertise in high-tech materials, in areas that extend beyond the field of tires,” said Christophe Rahier, Director of the High Technology Materials Business Line at Michelin. “In particular, by promoting the use of innovative recycled materials from tires in a variety of non-pneumatic industrial sectors.”
Michelin’s recycling goals may be ambitious, but it has plenty of ideas for how to achieve them, including new partnerships and identifying new ways to recycle tires and outlets for recycled tires. In 2017, the company, in partnership with Aliapur, held a Hackathon that challenged participants to come up with ways to use recycled tires. The winner of the Hackathon was a concept called “Black Pillow,” which proposed creating urban furniture from tire granulates.
If Michelin achieves its goal of 80 percent sustainable materials and 100 percent of tires recycled, the benefits will be staggering. The savings will be equivalent to:
– 33 Million barrels of oil saved per year (16.5 supertankers), or 54,000 GWh
– One month of total energy consumption in France
– 65 billion kilometers driven by an average sedan (8 L/100 km) per year
– All cars in Europe driving 225 kms (291 million kms), or 54 kms for all cars worldwide (1.2 billion cars estimated)
Michelin will also continue to develop its Vision concept. The tire’s tread will be manufactured and renewed using 3D printing, and the tire will be airless and made of biologically sourced and recycled materials. The high-tech tire will have a connected ecosystem within it that provides services and advice to the driver, and presents a solution that reduces the environmental footprint – or tire print – of cars.
Resource:3dprint.com
3D Science Valley Review:
What interesting about 3d printing appliction in tire making industry is that 3d printing is impacting this industry in two aspects.
Tire mold making is undertransforming by applying selective laser melting process to make more complex geometries of the mould, hence to make high performance tire afterwords.
And 3d printing polymer method as mentioned in the above article is pushing the tire making one step further, that is to say to skip the process of tire mould.
Recent Comments